Specifications
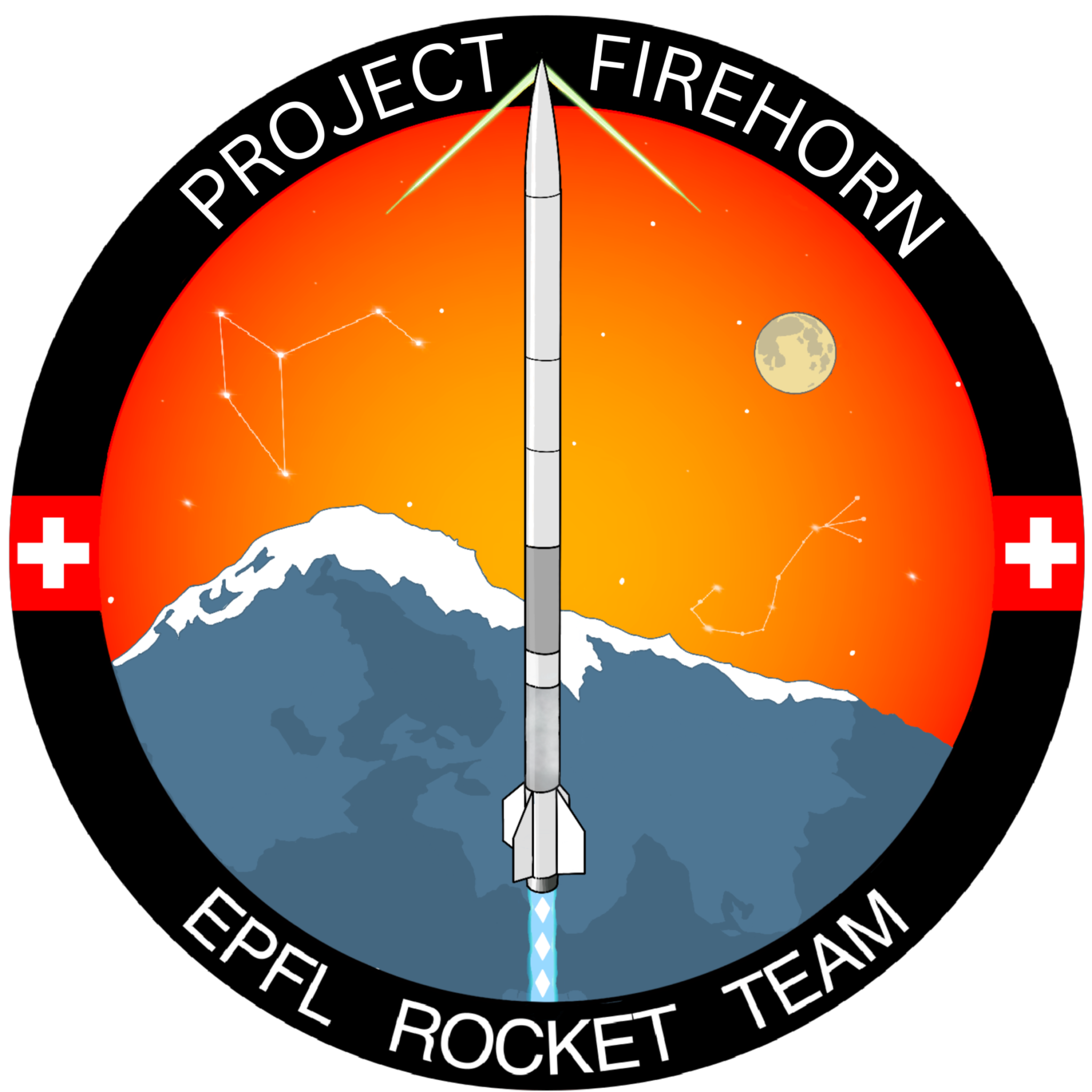
Highlights
Rocket components
Made from CFRP (Carbon Fiber Reinforced Polymer), the nosecone houses the payload and supports the Acoustic Levitation Scientific Experiment. CFRP provides high strength and low weight.
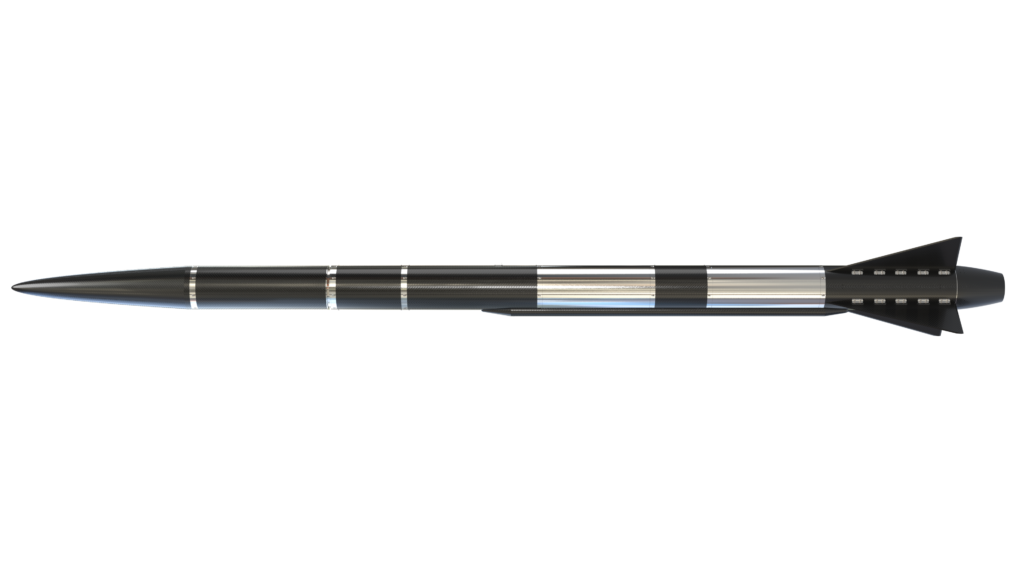
Constructed with CFRP, this bay contains the reefed parachute and is designed to handle over 30g deceleration forces.
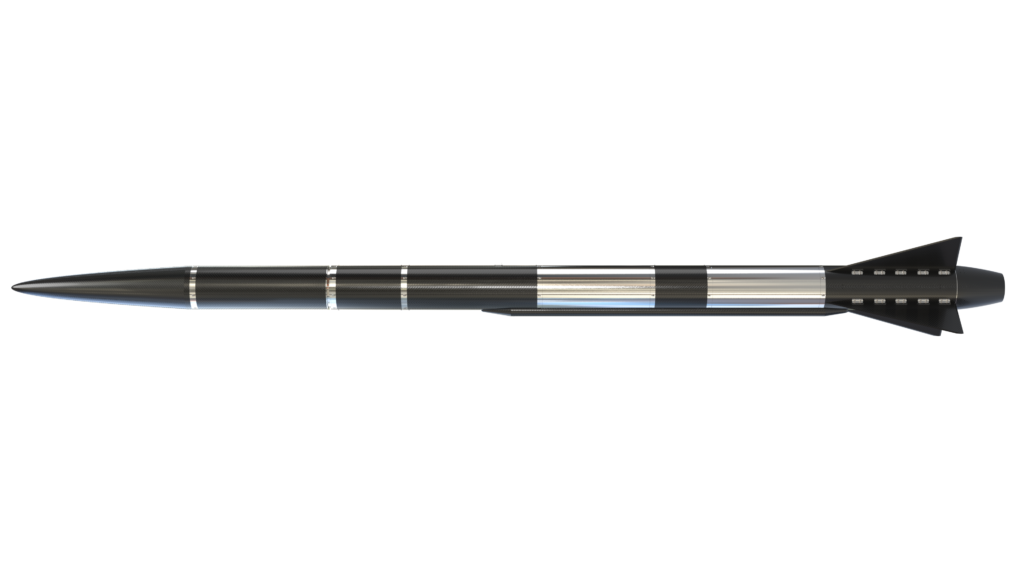
Built with GFRP (Glass Fiber Reinforced Polymer), this section includes omnidirectional antennas and the flight computer for controlling the rocket.
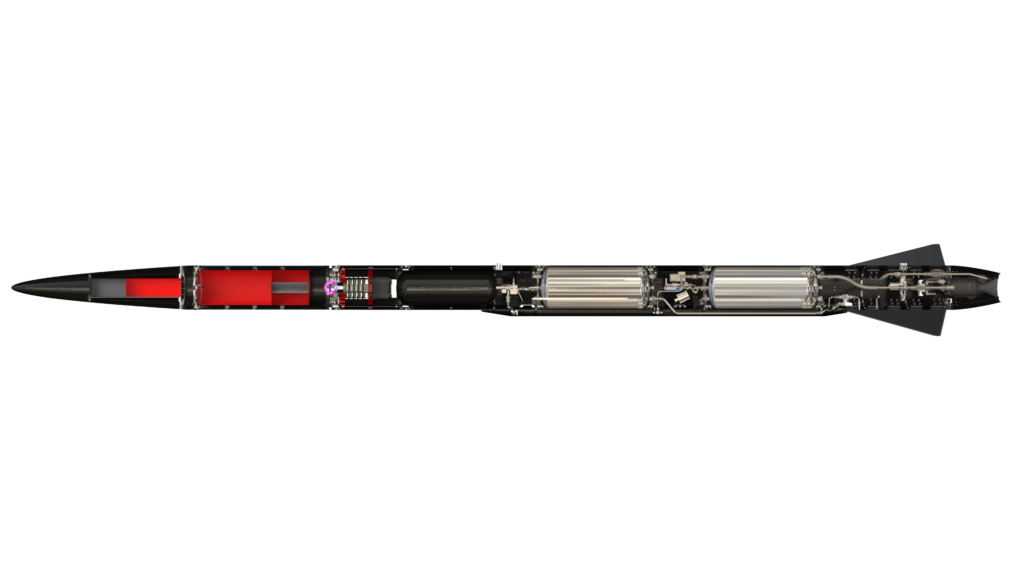
Equipped with a 400-bar COPV (Composite Overwrapped Pressure Vessel) and a Bang-Bang Pressure Regulator to manage pressure during flight.
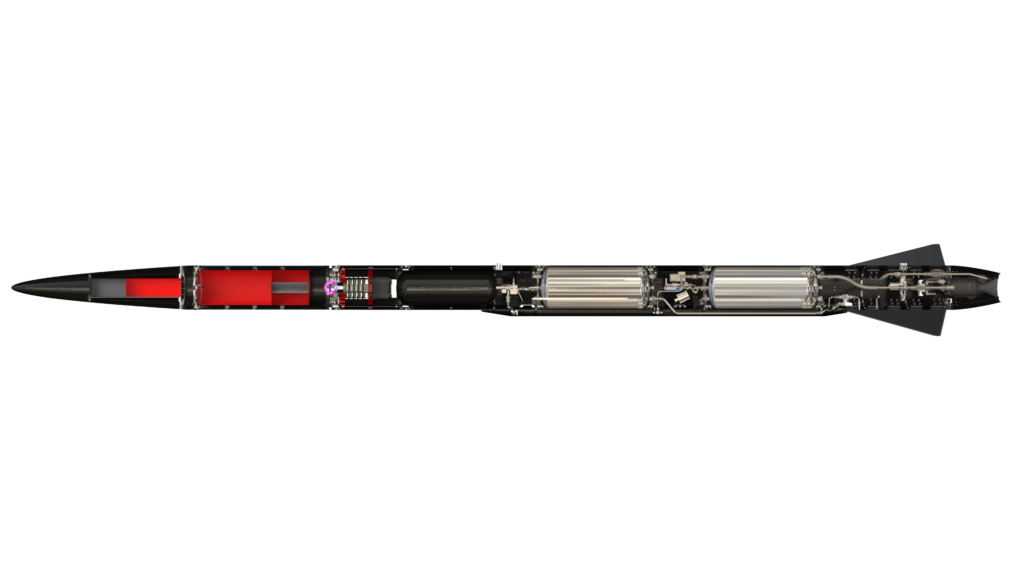
Made of 2050 and 2195 aluminium, the tanks are rated for over 60 bar operational pressure. CFRP aerocovers protect external plumbing, and integrated flight cameras monitor the system.
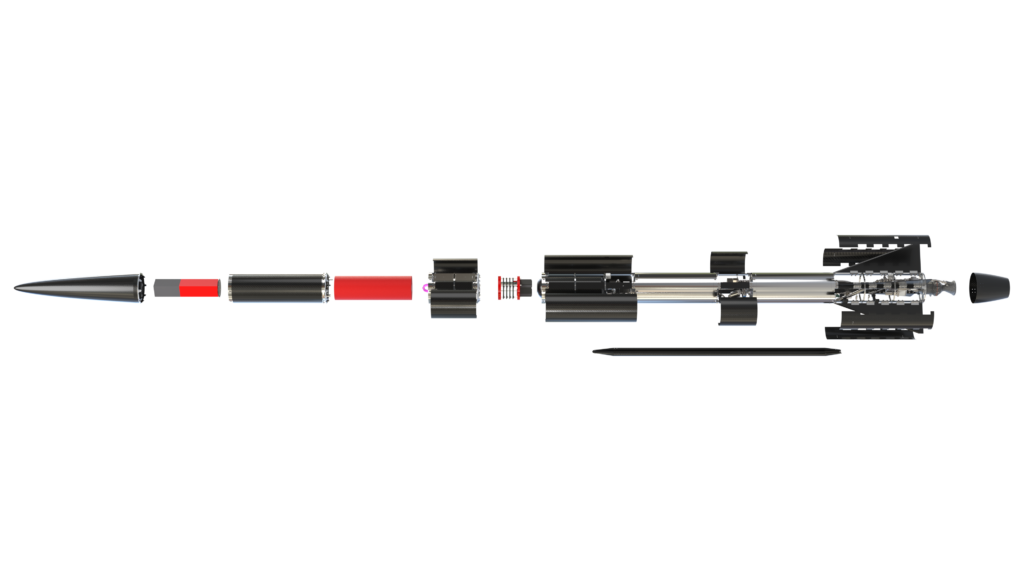
The internal structure includes CFRP rods, anti-buckling rings, and 3D-printed interface rings for added support and durability.
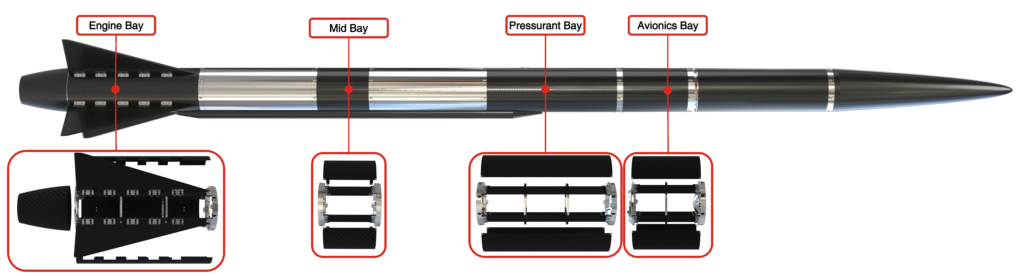
Home to the 7.5kN Ethanol-Liquid Oxygen engine, this bay features cryogenic-rated plumbing, valves, and CFRP fins. It interfaces with the ground segment for launch operations.
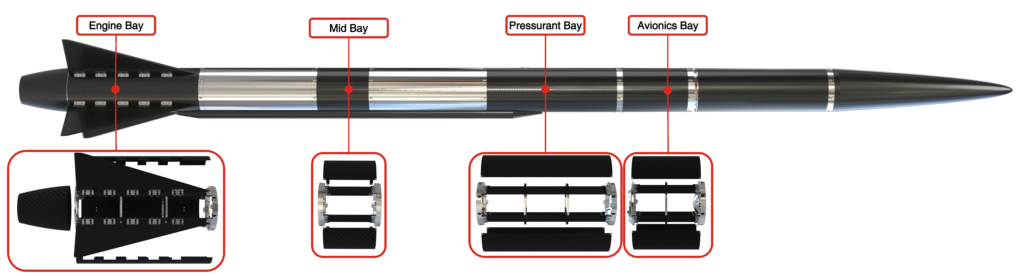
Animation
Milestones
One of the significant milestones to our journey was the project’s PDR (Preliminary Design Review) held in March, where stakeholders were presented with the initial vehicle design. A comprehensive PDR documentation, covering the technical design and project management details since September, totaling 267 pages, has been sent to stakeholders. In parallel, work on assembling a preliminary CAD model of the Firehorn rocket is underway, providing a tangible visualization of previously abstract technical requirements.